The BioReSteel project has been organized into six work packages covering the entire chain. The WP2 is biomass residues mapping, characterization and upgrading from lab scale. WP3 is to prepare and produce biochar which is derived from the chosen biomass residues for pilot tests in WP4 and short-term industrial tests in three EAF plants to verify the concept. The value chain and sustainability study are carried out in WP6. WP1 focuses on structuring the work in terms of coordination and management as well as dissemination, communication, and exploitation of the obtained results.
The BioReSteel approach is based on the consortium’s strong scientific and technological partnership in upgrading biogenic residues (Ingelia, UPV), characterizing (KTH) and testing/validating (Swerim, ORI, FENO, Celsa, SSAB) alternative energy carriers in EAF process which are complemented by life cycle assessment (LCA at RWTH), techno-economic analysis (Swerim), process simulation (CSM, RWTH) and safety management and control (FENO).
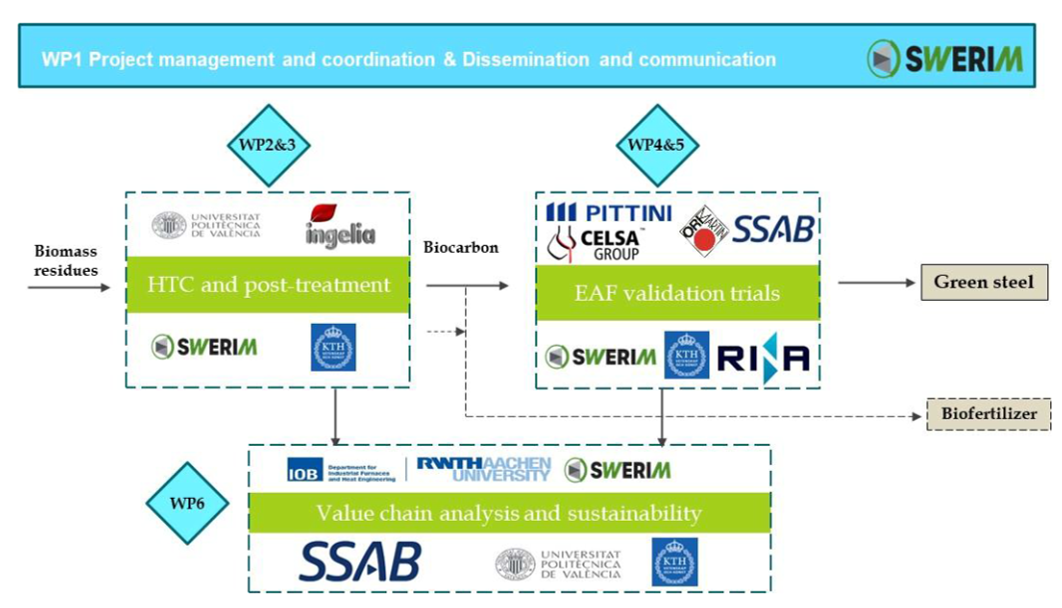
Partner | Main tasks in BioReSteel |
---|---|
![]() |
Swerim is the project coordinator. For the research work, Swerim contributes on hydrochar briquettes development and performs the pilot trials in its 10-ton EAF testbed. For the industrial trials at Celsa, Swerim takes part in the lance design, trials planning and on-site sampling of dust in the off gas. Swerim assists on theoretically evaluating the industrial trials and predicting the benefits of utilizing hydrochar. |
![]() |
SSAB assists Swerim for the pilot EAF trials, providing iron oxides for the bio-agglomerate. SSAB joins the techno-economical analysis in the BioReSteel project. |
![]() |
RWTH-IOB is in charge of investigating the integration of the HTC process into the steelmaking process, developing a mass and energy balance-based model simulating the heat integrated HTC production are its main activities. Additionally, RWTH-IOB contributes to the sustainability assessment and benefits analysis especially via the LCA analysis. |
![]() |
Ingelia main task is to produce 100 t of pristine hydrochar from garden prunings and forest residues and pelletize it for the transport. The hydrochar is treated via acid leaching to remove phosphorus. In addition, 63 ton hydrochar will be treated thermally at 600 °C. Ingelia participates in the elaboration of the safety recommendations for hydrochar handling and storage. |
![]() |
FENO: The main activity in the project is related to industrial tests in EAF (150 ton) using densified hydrochar pellets via top charging: preliminary evaluation of safety conditions of handling, stocking, and fluid transport; execution of tests, collection of data, evaluation of results. |
![]() |
CSM is involved in following activities:
|
![]() |
KTH has extensive research experience in the application hydrochar for various metallurgical processes. In this project, KTH is involved in:
KTH performs laboratory experiments for characterisation of materials (physical, chemical and metallurgical properties) used for pilot and industrial trials and their effect on quality of the final obtained steel. KTH attends pilot and industrial trials and collects samples (steel and slag) for investigations and analysis. |
![]() |
CELSA run hydrochar injection tests in their industrial furnace and assists Swerim to perform the pilot trials. |
![]() |
Ori Martin produces bio-agglomerate by using hydrochar and mill scales. The bio-agglomerates will be top charged into the industrial EAF to recycle the mill scale and increase the steel yield. |
![]() |
UPV is involved in biomass mapping, biomass selection, and its hydrothermal carbonization; it studies the phosphorus extraction and the production of a solid inorganic macronutrient fertilizer at a laboratory scale, complying with the EU regulation. UPV is involved in the hydrochar finishing and characterization.
C leads the feedstock characterization and selection, carries out lab scale experiments for the
technical assessment of Ingelia and evaluates the possibility to recover phosphorus from the
carbonaceous materials. |